Understanding Welding WPS Requirements: Finest Practices and Techniques for Quality Welds
In the world of welding, understanding Welding Procedure Requirements (WPS) requirements is a vital component that directly affects the high quality and honesty of welds. Complying with these criteria makes sure uniformity and reliability in welding outcomes. Nevertheless, achieving quality in welds surpasses simply recognizing the requirements; it involves applying finest techniques and methods that raise the craft to a level of accuracy and ability that distinguishes the average from the exceptional. As we browse through the details of welding WPS criteria, discovering key understandings and strategies for accomplishing top-tier welds will be extremely important for welders looking for to excel in their craft and produce welds that stand the examination of time.
Understanding Welding WPS Specifications
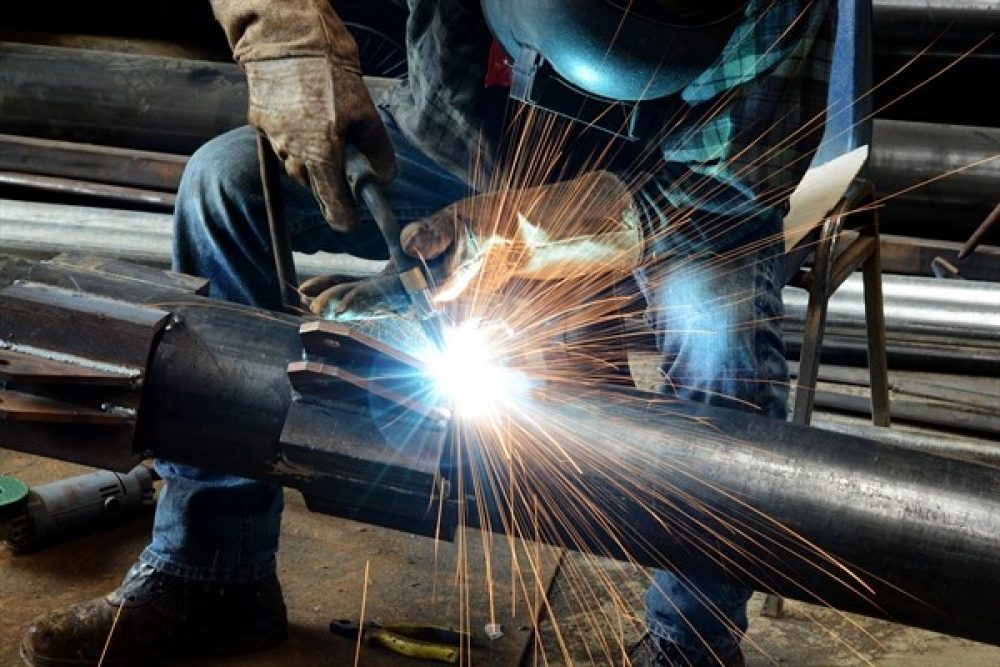
Understanding WPS criteria is vital for examiners, welders, and engineers included in welding procedures. By adhering to WPS guidelines, welders can produce welds that meet the needed mechanical residential properties and structural honesty. Inspectors count on WPS documents to validate that welding procedures are being adhered to properly and that the resulting welds are of excellent quality. Designers use WPS requirements to make welding procedures that guarantee the resilience and dependability of bonded frameworks.
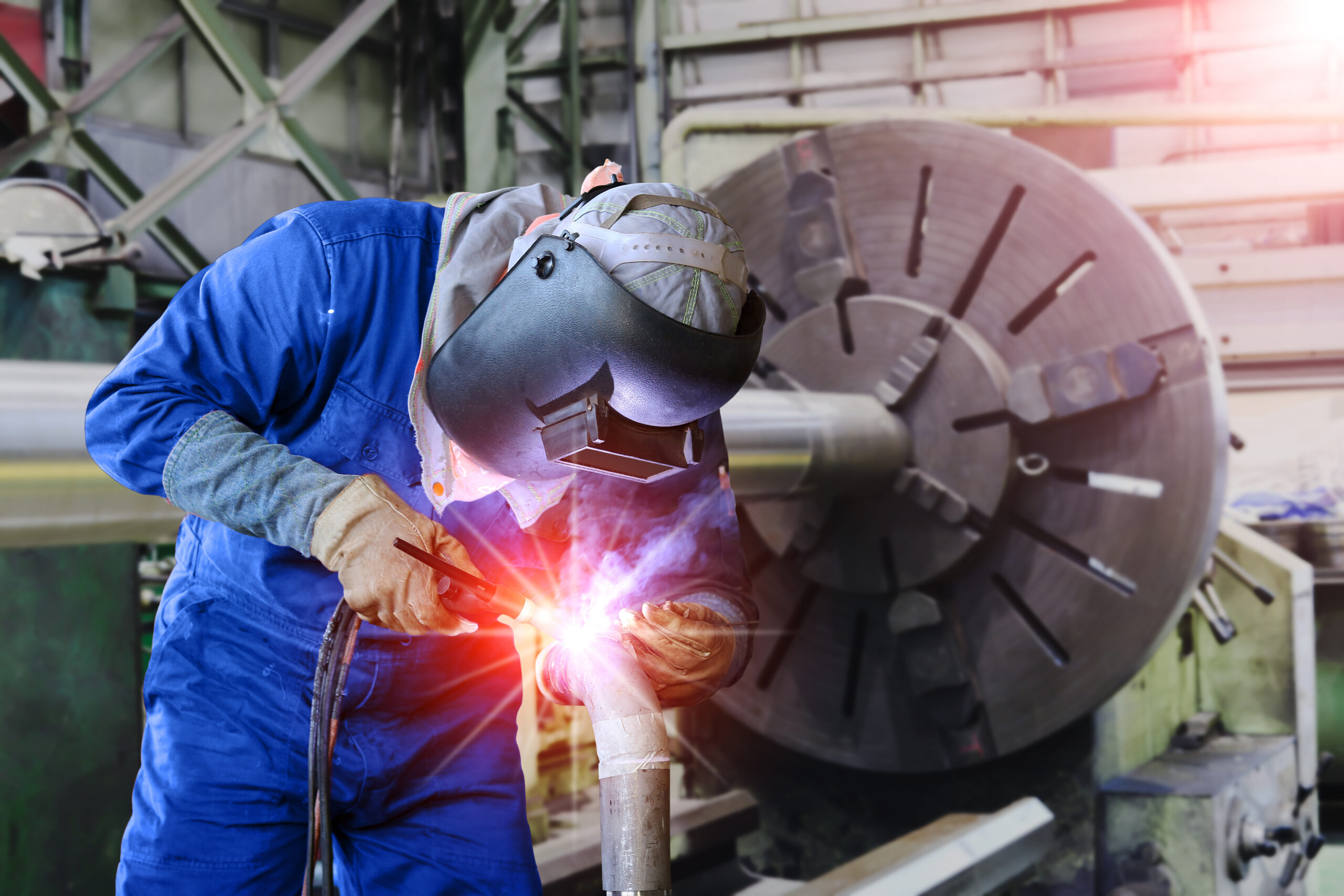

Important Tools for Top Quality Welds
Understanding welding WPS standards is crucial for welders to efficiently use the necessary tools required for producing quality welds. The type of welding maker required depends on the welding procedure being used, such as MIG, TIG, or stick welding. Cord brushes and cracking hammers are crucial for cleaning the weld joint before and after welding to eliminate any impurities that could influence the high quality of the weld.
Secret Techniques for Welding Success
To attain welding success, one should grasp the crucial methods necessary for creating premium welds. Preserving a steady welding and a stable hand placement throughout the procedure is essential to accomplishing accuracy and consistency in the welds. By mastering these essential strategies, welders can boost the top quality of their job and accomplish welding success.
Ensuring Conformity With WPS Specifications
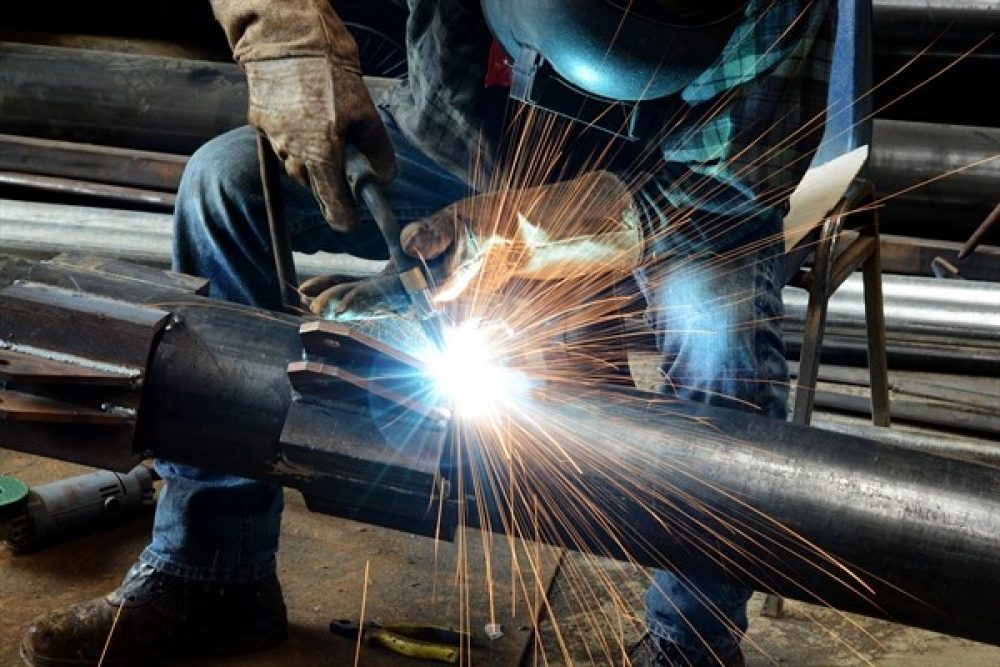
Furthermore, welders must undertake training to familiarize themselves with the WPS criteria pertinent to their job. Regular audits and examinations should be conducted to verify that welding activities align with the suggested WPS standards. In addition, keeping thorough documents of welding criteria, equipment calibration, and evaluation results is crucial for showing compliance with WPS standards - welding WPS. By carefully adhering to WPS anchor requirements, welders can guarantee that their work meets the necessary quality levels and contributes to the total success click for source of the welding task.
Troubleshooting Common Welding Issues
When confronted with typical welding issues, identifying the source is vital for efficient troubleshooting. One common trouble is the presence of porosity in welds, typically triggered by contaminants such as moisture, rust, or oil. To resolve this, making sure proper cleansing of the base metal before welding and using the right shielding gas can dramatically minimize porosity. Another issue frequently experienced is lack of combination, where the weld fails to correctly bond with the base product. This can come from poor warm input or inappropriate welding technique. Adjusting specifications such as voltage, cable feed speed, or travel speed can help enhance combination. Furthermore, distortion, cracking, and spatter are common welding obstacles that can be minimized via proper joint prep work, constant warmth control, and selecting the proper welding consumables. By thoroughly comprehending these typical welding issues and their source, welders can effectively fix issues and accomplish high-grade welds.
Verdict
Finally, mastering welding WPS criteria calls for an important source extensive understanding of the guidelines, using crucial tools, and applying vital strategies for effective welds. Making certain conformity with WPS standards is vital for creating quality welds and avoiding common welding issues. By adhering to ideal methods and techniques, welders can achieve reputable and regular cause their welding projects.
In the world of welding, understanding Welding Treatment Requirements (WPS) standards is a vital element that straight influences the high quality and integrity of welds.When delving into the world of welding practices, an essential facet to comprehend is the relevance and details of Welding Procedure Spec (WPS) standards. WPS criteria offer a detailed standard for welding operations, ensuring uniformity, quality, and safety and security in the welding procedure. The type of welding equipment needed depends on the welding procedure being utilized, such as MIG, TIG, or stick welding.Achieving welding success via the mastery of vital methods requires a complete understanding and adherence to Welding Procedure Specification (WPS) standards.